Are you someone who has been thinking about getting your music professionally pressed on custom vinyl records? Do you want to cut the costs of short-run records by pressing your own? Are you frustrated by how imperfectly you think your vinyl records come out on the other end of the process?
This blog is for you if these are the questions you have. This article aims to give you some tips on the process of pressing your own records and let you choose between DIY or going for a professional approach.
Why Should You Press Your Own Vinyl?
Did you know that you can press your own vinyl records and distribute them yourself? However, even if you are on the lookout just to spread your music to some local friends, you can!
In this digital age, music lovers are turning their attention back to one of the oldest formats of music delivery around vinyl records. While digital music can sometimes sound a bit flat, there is something about customised vinyl record that makes the songs seem fresh and clears out any cobwebs that might have been accumulating on your earbuds from the commute to work.
If you are a hip-hop artist, audiophile, or just someone who is super passionate about vinyl, then you have probably been there. Your record might be spinning today but after a few plays it begins to skip, the needle jumps off the vinyl, or it randomly stops playing entirely. This will happen with few records and is a result of poor-quality control during vinyl record pressing.
Important Tips to Press your Vinyl Records Efficiently
Essentials before Pressing your Vinyl
Get the master recording done by an audio professional for a vinyl record. This is because vinyl records have different characteristics compared to CDs or MP3s. It also has different frequencies and dynamic range which makes them sound better than other formats. So, in order to achieve this, you need someone who knows how to master for vinyl records only.
Once you have created your master recording, it will need to be converted into a vinyl format. Find a reliable vinyl manufacturer and get pricing quotes from various producers.
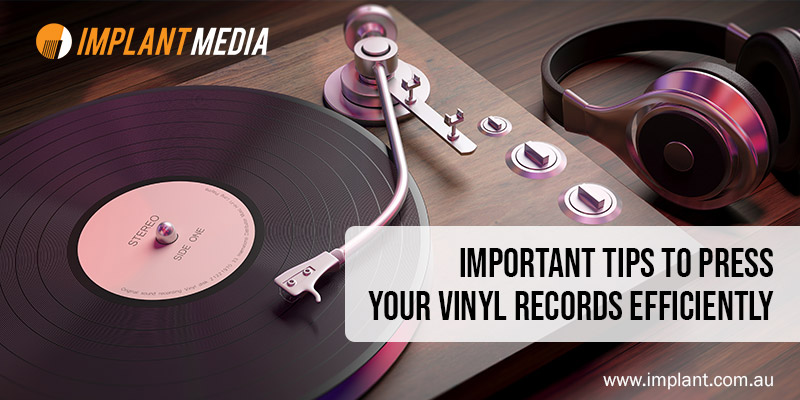
Design your Record Labels Carefully
- Your label should include all the information required by law, such as artist name and song titles. Additionally, make sure that all the information is legible and easy to read.
- Make sure your vinyl record sleeve design is of the finest quality. When printed on contoured paper or cardboard, the print must be clear and crisp to avoid appearing pixelated or blurry.
- Pick out your colours with care. If you like, you may incorporate different colours in your layout if they complement the others well and do not overpower them. If you are using two colours, experiment with blending them on screen by combining different tones of each colour (for example, blue and purple).
- When printing in black ink as opposed to white ink, use easy-to-read fonts or make the text larger than usual to make it easier to read.
Understand the Various Vinyl Record Formats
There are several different sizes of vinyl records that can be pressed at different prices depending on how long they last and how much space they take up on an album cover or sleeve. These formats include 7, 10 and 12 inch vinyl records.
Understand the Various Processes of Vinyl Record Production
If you are thinking about pressing vinyl records, you will want to know what the various processes are and how they fit together. Here is a quick rundown on the most common steps in pressing a record:
Cutting
In this process, a master record is created from which all other copies will be made. This can be done using a lathe or a laser. Cutting can be done by an outside source or at your own facility if you have the equipment.
Galvanization
This process turns the negative image of the master into a positive image that can be used on press plates. Galvanization is performed by electroplating nickel onto the master disc before it is cut into stampers for pressing vinyl records.
Pressing and pocketing
The stampers created from galvanization are placed in presses where they are heated and pressed against vinyl discs called blanks to create grooves in their surfaces. After pressing, each disc is then put in its own protective sleeve called a pocket with all of its identifying information printed on it before shipping out to stores or artists.
Wrapping Up
The process can be frustratingly complex and mind-numbingly confusing at times. But before you give up, do not let it go just yet. Choose Implant Media for all your custom vinyl record needs. We only work with the best digital record cutting equipment, whether you are pressing a single or running an entire record label, we have the knowledge and expertise to produce your project in a timely manner.
Visit our website to know the different types of vinyl pressing services we offer.